Zoom in on one of the solutions for drastically reducing the vacuum in parcels.

Automated carton packaging solution
Nature abhors a vacuum… And it’s not the only one! On average, 43% of a dispatched parcel is empty*. When the 370 senior managers questioned estimated it at only 25%, this shows just how high the stakes are and how many areas there are for improvement.
The figure is as high as 51% for groceries and 52% for toys.
Yes, who hasn’t complained about receiving their beautiful new toothbrush in a box ten times too big, with all that this implies in terms of carbon footprint, use of packaging and simply the impact on the company’s brand image.
75% of customers admit that the environmental impact of a product’s packaging affects their purchasing decision**.
And the study dates from 2018 !! Imagine 2023.
Processes can be improved by far, and fortunately solutions do exist. That’s what we’re going to talk to you about today, focusing on the benefits of automated cardboard packaging solutions.
This innovative packaging solution is aimed primarily at e-tailers and logistics specialists. The main challenge is to improve efficiency on several levels.
Preamble
As a preamble, the first observation is that these vacuum reduction options are already forcing designers to take this parameter into account in their specifications. And this, by considering the following question:
- How to guarantee maximum protection, such as absorption of micro-vibrations and shocks with resilience, in a very limited space.
- Or in other words: how to reconcile maximum protection, reduced cushioning and its cost impact (use and weight).
Note that this point was taken into account from the outset in the Blocbox® and Ouatbox® specifications.
Resilience and shock absorption have always been priorities in the development of our solutions. The expandability of cushioning wadding makes it possible to combine reduced space with “close” protection.
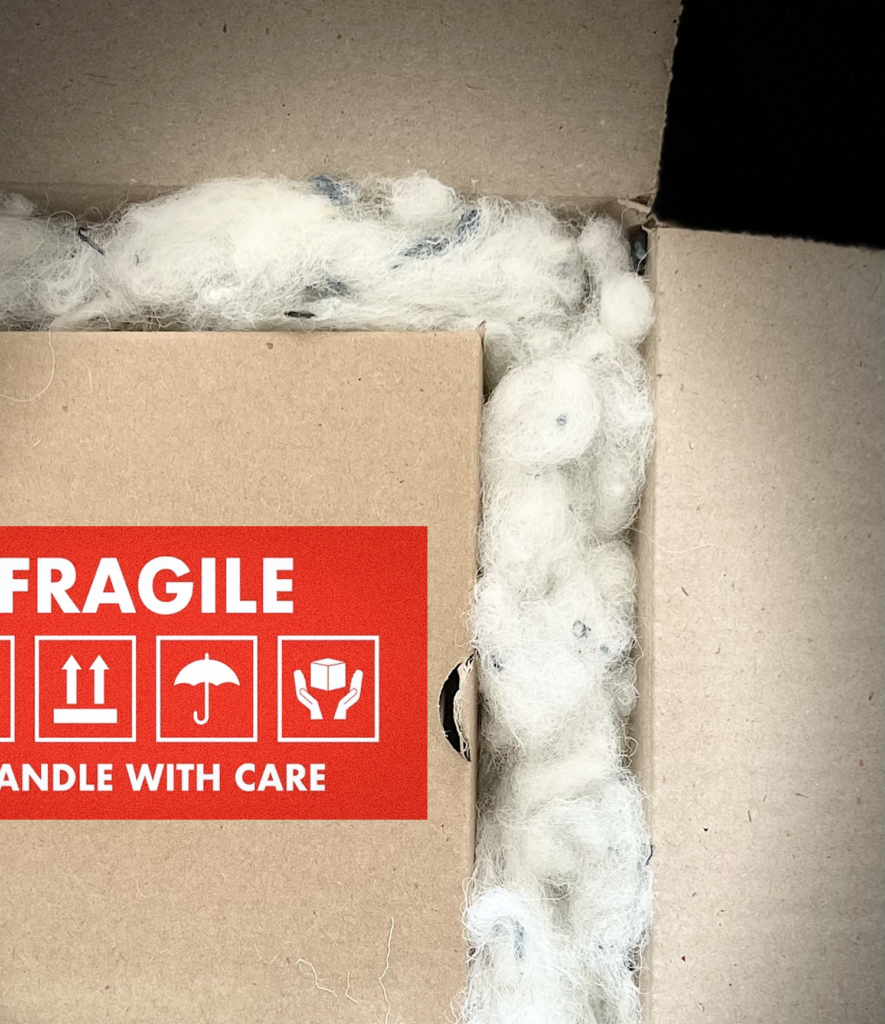
Let us now illustrate the advantages and constraints to be taken into account with this type of machine : automated solutions for made-to-measure cardboard packaging.
There are many players offering this type of solution, so we won’t go into detail about all the technical features of each machine, but rather try to highlight the main points to bear in mind.
How these automated solutions work ?
There’s nothing like a few selected videos to demonstrate the benefits of the solution for certain types of product.
Here we present 4 players in the sector :
- Example Quadient (ex Neopost) (machine types: CVP 500/ Impack/ Everest) :
https://www.youtube.com/watch?v=6W0CHP9FQFY
- Exemple CMC (type machine : Cartonwrap XL) : https://www.youtube.com/watch?v=U1yw05mWnXw
- Exemple de Panotec (types machines : Compack EVO/ Opéra/ Nextpro) :
Cardboard manufacturers such as DS Smith have also taken up the issue.
Exemple DS Smith ( Made2fit) : https://www.youtube.com/watch?v=TsSmEwFt3cs
What are the advantages and constraints ?
Benefits :
- Major logistics optimisation
- Savings of up to 50% on parcel volume, and in some cases almost 100%; imagine the impact in terms of transport savings on volume weight.
- It’s bad enough that a single cm can push you into a higher price category ! https://www.colisconsult.com/2020/02/03/poids-volumetrique-transport/
- Optimising truck loading
- 32% reduction in transport costs***.
- Saving storage space
- 10% more productive than manual packaging
- Operator time reduced by up to 88%***.
- Savings on consumables
- Up to 20% of material (cardboard) saved ****
- Reducing MSD for operators
- Adaptable for single or multiple items
- Adaptable to items of all shapes
- Consumer image
To sum up, most of the savings will be made on :
- Optimising transport
- Operator time
And when it comes to consumables, the gains become significant when the volume of parcels to be dispatched is very high.
Constraints :
- Not suitable for personalised packaging used for striking, olfactory unboxing or noble, personalised cushioning materials.
- If there is a need for cushioning and protection for fragile objects, unless pre-packaging is available.
- This is a substantial investment, which is not, of course, suitable for all players and which needs to find its point of profitability. Obviously, each case is unique and needs to be fine-tuned, but it can be estimated that ROI can be achieved after 24 months.
Conclusion
Logistics for the sake of efficiency, but also constant pressure from end consumers, combined with rising transport costs, are pushing these solutions in the right direction.
They are not suitable for everyone, particularly in terms of speed and investment, but if they are adapted they can lead to significant savings, including in terms of environmental impact.
On a global scale, the savings linked to the reduction of the void could amount to 46 billion dollars*, which would give us plenty of reason to continue our cross-disciplinary work on this issue!
Sources
*According to Forbes insight and DS SMITH.
**Coleman Parkes Research (for pro carton) 2018 survey of 7,000 people
***According to the website Material handling 247 https://www.materialhandling247.com/product/cvp_500_automated_packing_system/
**** According to the Sparck technologies website https://sparcktechnologies.com/fr/cvp-impack-solution-emballage-automatique/